Benefits of Building Automation Systems
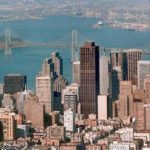
Benefits of Building Automation Systems
Lowers Utility Costs: Building Automation Systems typically save 15% of the operating costs of the equipment. For most buildings, this results in savings that range from $0.20 to $0.40/ ft².
Maintains Measured Comfort: Computerized controls help to maintain even temperatures and lighting levels within the facility to provide measured comfort. Maintaining consistent temperature and lighting levels cuts down on wasted energy.
Enhances Property Value: The value of most commercial buildings is related to the net operating income. Lowering utility costs increases the net operating income on a dollar for dollar basis. Every $0.10/ ft²saved in energy could increase the market value of the property by $0.80/ ft². A 100,000 ft² building could increase in value by $120,000 by reducing energy costs $0.15/ ft².
Reduces Occupant Complaints: A more comfortable building means fewer occupant complaints. This means less time resolving complaints, happier occupants, and a more productive business environment.
Increased Productivity: Better ventilation and air quality improve greater worker productivity and less sick time. The value benefits average $25.00/ ft². With decreased sick days translated into a net impact of about $5.00/ ft²and increased in productivity translated into a net impact of about $20.00/ ft².
Simplifies Building Operation: Computerized controls and real time graphical displays let you see exactly what is happening with the equipment in the building without having to go up on the roof or crawl up into the ceilings. This saves on costly troubleshooting visits, and simplifies operations.
Reduces Maintenance Costs: Running the equipment less and controlling it better reduces wear-and-tear and keeps maintenance costs down, and extends equipment life.
Avoids Business Interruptions: Unexpected equipment breakdowns can cause costly business interruptions. The cost of employees and/or processes in a building can be 75 to 100 times the facility operating cost on a square foot basis. The impact when customers are involved can be even more costly. Breakdowns and emergency repairs are very expensive. Computerized controls monitor equipment status and help you head-off unexpected problems.
A Great Investment: Most systems will pay for themselves in less than two years.
Typical numbers for an owner-occupied 100,000 ft² building would be as follows:
- Total system cost $200,000 ($2/ ft²)
- Utility Company rebate $30,000 (15% rebate)
- Annual energy savings* $15,000 (15% savings)
- Annual productivity loss avoidance * $50,000 (1% savings)
- Annual O & M cost avoidance* $10,000 (10% savings)
- Simple payback 1.3 years
*Annual cost avoidance year after year.
How Does Building Automation Work?
HVAC and Lighting Controls: Stand-alone computerized controllers are installed to take over the control of building HVAC (heating, ventilation, and air conditioning) systems and lighting. The building is not only scheduled more closely but it is also operated more intelligently and efficiently.
Outside Air Optimization: The proper control of outside air provides necessary inside air changes for occupant comfort and health, minimizes energy costs by space pre-conditioning, allows for enthalpy-based free cooling (Learn more about Enthalpy), and reduces the use of outside air when it is not needed.
Coordinating Equipment: Orchestrating the operation of building systems, so that equipment works together, saves energy and improves comfort. Individual control systems that are not centrally monitored and coordinated can fight each other or malfunction, causing comfort problems and wasting considerable energy. BACnet based BAS can interface to existing or planned systems so that the building will run smoothly and at peak efficiency without expensive duplication of controls or unnecessary complexity.
Graphical Operation: Simplifying facility operation and integrating data from various systems in a unified manner is best accomplished with a graphical user interface. This eliminates the need to memorize commands or point numbers, and allows the operator to take a walking tour of the facility from the console. Existing systems can be easily upgraded to add this powerful operational tool. Point and click graphics empowers management by letting everyone see what is going on and taking the mystery out of proper operations.
Direct Digital Controls (DDC): Upgrade older existing equipment to DDC to match new equipment functionality. These controllers come standard on most new mechanical equipment and are more reliable, require less maintenance, provide more sophisticated control, and are less expensive to purchase and operate.
Tighter Scheduling: Conventional controls, such as analog time clocks, are inaccurate and are typically setup to run equipment longer than needed. By automating this function with computerized controls, the computer can predict the optimum time to start/stop equipment based on an astronomical smart schedule and eliminate waste caused by excessive runtime.
Smarter Control: HVAC equipment is typically sized to handle the building load under worst-case scenario (conditions). Most conventional controls are set up to always meet these design criteria. With the automation system, control set points and strategies can be adjusted to meet only the actual load, eliminating unnecessary waste.
Interested in implementing commercial building controls?
Lite Rite Controls specializes in lighting controls which can integrate into your building automation system. We have Lutron Vive and Crestron Zum, systems that are scalable and easy to use. Contact us to learn more.
Visit – Lite Rite Controls
Call us at (562)294-0660
or
Email at info@literitecontrols.com or jerimiah@literitecontrols.com